Scaling Smart: Selecting the Right Manufacturing Method for Your Product
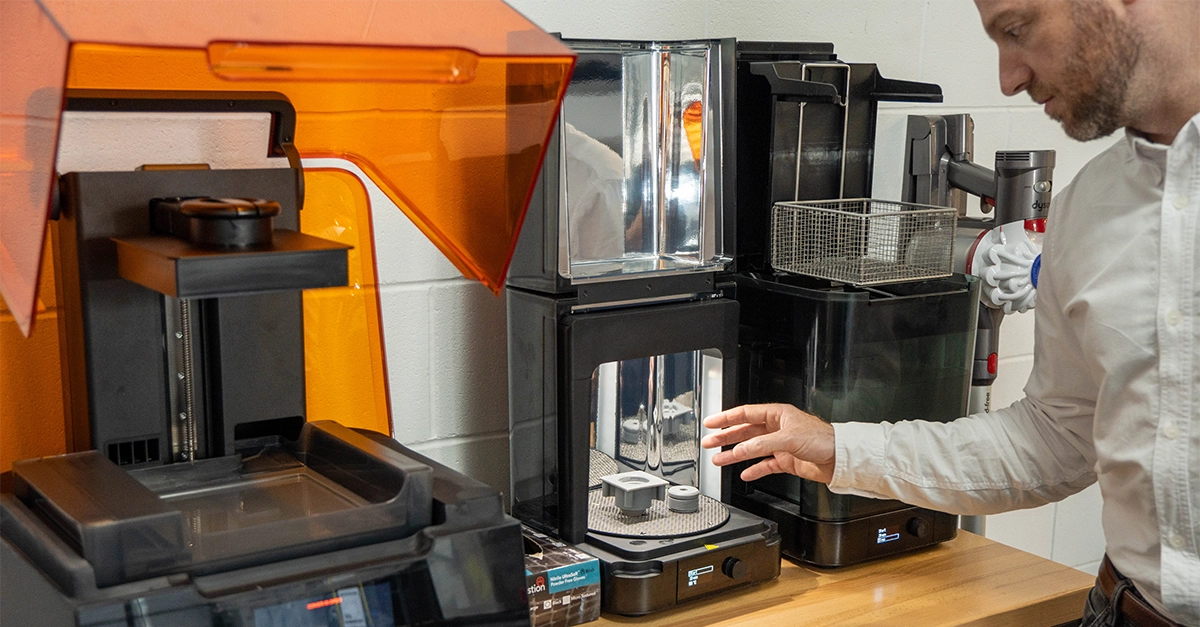
Every great product starts the same way—with a spark of an idea. But what happens next can make or break its future.
Will it emerge quickly, tested and refined with precision? Or will it stumble in a tangle of poor choices, high costs, and missed opportunities?
This is the hidden battleground of industrial design: prototyping and manufacturing. The tools you choose in this stage determine how fast you move, how much you spend, and whether your product even makes it to market. And while the options are vast, each one comes with trade-offs that can either accelerate your vision—or undermine it.
Let’s break down the most common techniques and methods, and explore the pros and cons that every designer, engineer, and founder needs to understand.
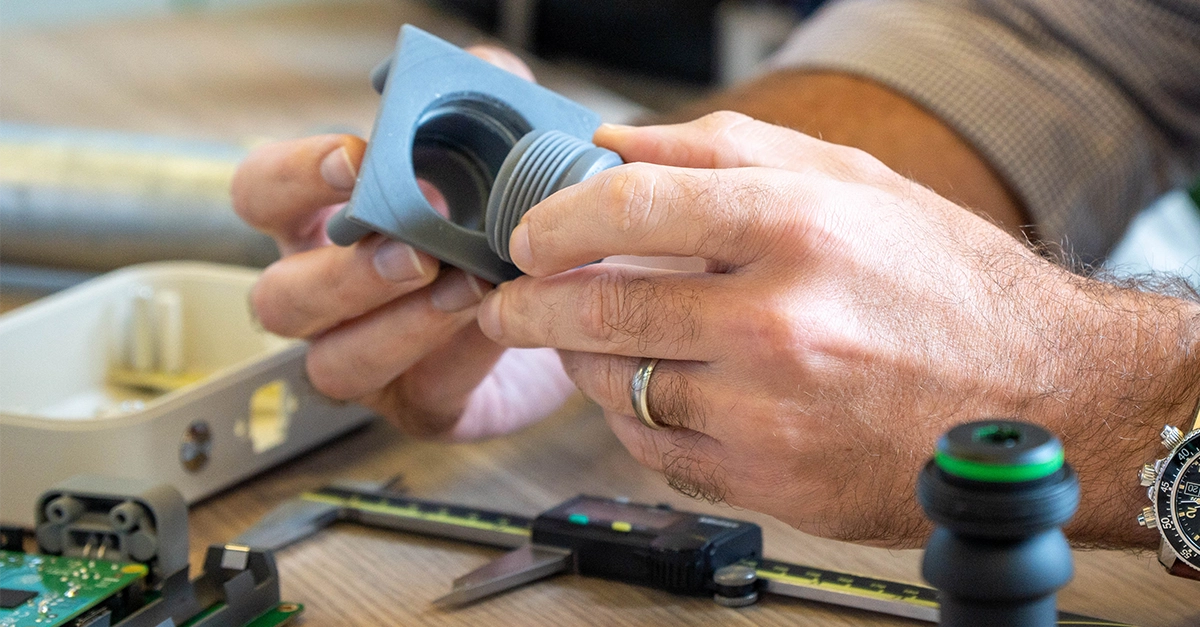
Prototyping Techniques
3D Printing (Additive Manufacturing)
Perfect for early-stage iteration, 3D printing allows you to quickly bring ideas to life. It handles complex shapes effortlessly and costs little to start. But while fast, it often uses materials that don’t match final production—meaning what works in a prototype may fail in the real world.
CNC Machining
When precision matters, CNC delivers. It’s ideal for functional prototypes made from real-world materials. It’s slower and more expensive than 3D printing, but far more accurate and robust—making it the go-to for mechanical validation.
Foam and Clay Modeling
These tactile, hands-on models are a designer’s best friend for exploring ergonomics and proportions. They shine in the concept phase but offer little insight into function or durability.
Urethane Casting
Bridging the gap between prototype and production, urethane casting offers quick, low-volume runs that look like moulded parts. It's fast, flexible, and affordable—until you scale.
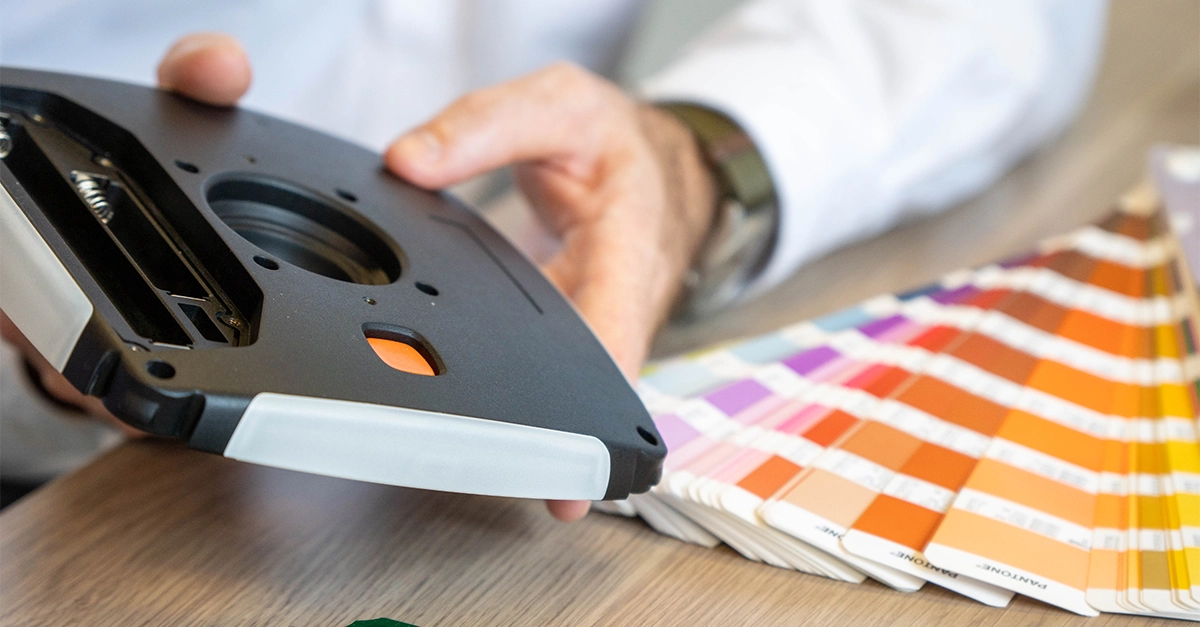
Manufacturing Methods
Injection Moulding
This is the powerhouse of mass production. Once the mould is made, parts fly off the line with speed and consistency. But get your design wrong, and the cost of changes skyrockets—tooling is expensive and inflexible.
Die Casting
For metal components, die casting offers high accuracy and finish at volume. It’s efficient—but like injection moulding, slow and costly to set up.
Sheet Metal Fabrication
Great for lower volumes, especially enclosures and structural parts. It’s fast and cost-effective, but less suited to complex designs.
The Payoff
So, what’s the right path?
The truth is, there is no single answer. But there is a right mindset: strategic selection. By understanding the tools at your disposal—and when to use them—you turn guesswork into clarity, cost into value, and risk into momentum.
There are of course so many other manufacturing techniques that can be utilised for low, medium, or high volume production, but the methods outlined here are the most used in our day-to-day operations at Ingenuity.
Every product walks a tightrope between vision and execution. Prototyping and manufacturing are the safety net—or the trap. Choose wisely, and that spark of an idea becomes a product the world can hold.
And that’s when the real story begins.